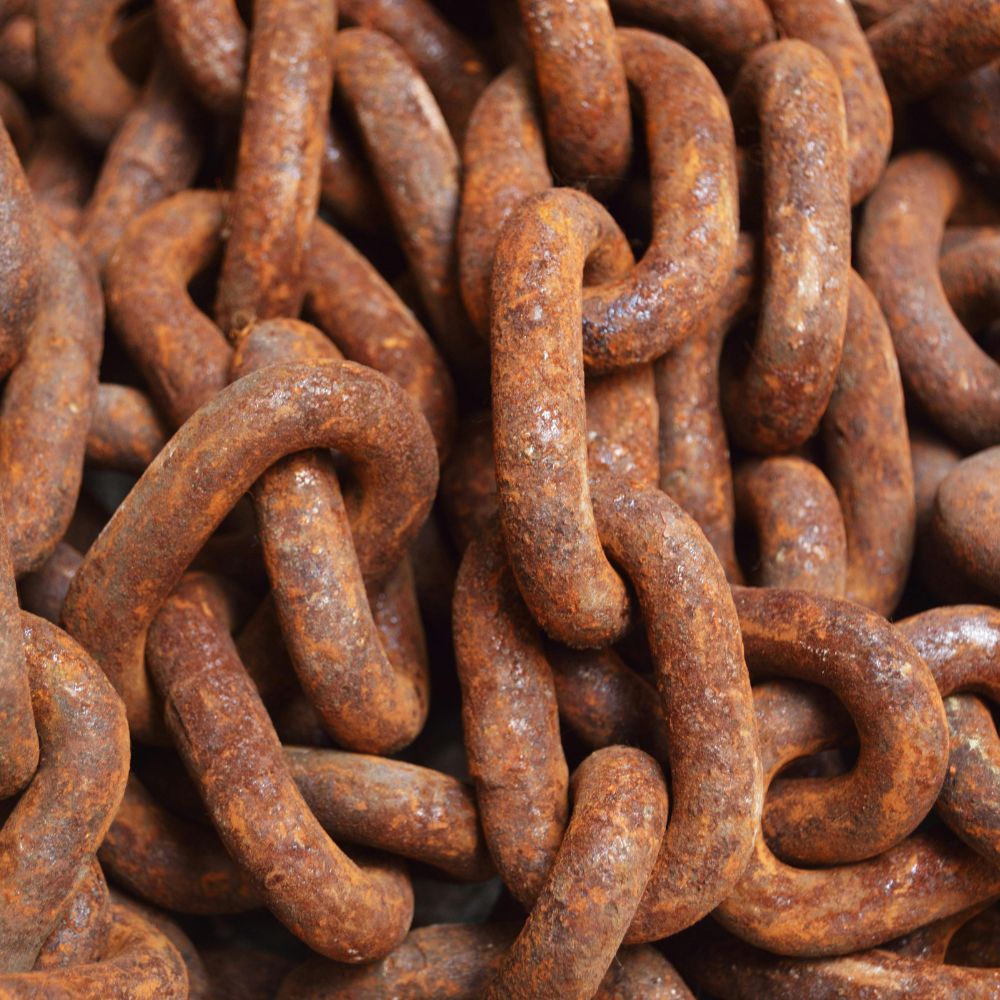
KORRÓZIÓ vs. MEGELŐZÉS
Ebben a bejegyzésben összeszedtük, amit a korrózióról és a korrózió védelmi bevonatokról tudni érdemes.
Mi az a korrózió?
A korrózió a szerkezeti anyagok környezeti tényezők és körülmények hatására bekövetkező károsodási folyamata. A korrózió legtöbbször több folyamat és kölcsönhatás eredménye. Mivel ezek a folyamatok sokfélék lehetnek, így maga a korrózió is igen sok féle lehet. Rövid ismertetőnk elsősorban a fémek és épületszerkezetek korróziós fogalmát és a festékbevonatokkal (azaz festékekkel és más bevonatokkal) történő korrózió elleni védelmét igyekszik röviden összefoglalni.
A hatásos és ellenálló bevonat kialakításához elengedhetetlen, hogy ismerjük a károsító tényezők az anyagra, valamint a bevonatra gyakorolt korróziós hatását. A fontosabb korróziós jelenségek eredetük szerint három csoportba sorolhatóak.
A kémiai korrózió – amely a szerkezeti anyagoknak az anyagok vegyi egymásra hatására bekövetkező káros átalakulása. Ezek például a
- rozsdásodás /vasanyagokon, oxigén és víz hatására/
- patinaképződés /rézanyagokon szén-dioxid és vízgőz hatására/
- reveképződés /fémek hő hatására bekövetkező oxidációja/
- füstgáz-korrózió /SO2, SO3, H2S, CO2, vízgőz, stb./
- atmoszférikus korrózió /légköri szennyeződések hatására/
- savak, lúgok, sóoldatok hatása
- hidrogén okozta korrózió /hidrogénridegség acélszerkezetekben/
- talajkorrózió/humuszsavak/
- fázishatár korrózió /vízfelszín közelében kialakuló korrózió/
Az elektrokémiai korrózió – amely a szerkezeti anyagok érintkezésénél, helyi galvánelem képződés következtében létrejött elektrokémiai folyamatok károsító hatása. Ezek lehetnek a
- galvánelem képződés /elektrolit, (pl. víz) jelenlétében egyes fémek között elektromos áramlás indulhat meg. (pl.: vas-cink, vas-ón, vas-réz, stb.)
- kontakt korrózió /egyes fémek tartós érintkezése közben az egyik fém károsodik (pl. vas-aluminium)
- szelektív korrózió /ötvözeteknél csak az egyik alkotórészt oldja ki a támadó közeg (pl. sárgarézből a cink)
Mechanikai korrózió a szerkezeti anyagok mechanikus és dinamikus erők hatására bekövetkező károsodása. Ezek lehetnek
- dörzskorrózió /egymással érintkező fémrészek felületein a gyakori elmozdulás 8pl. rezgés) hatására bekövetkező roncsolódás
- erózió /áramló gázok, gőz és az azokban lebegő szilárd részek mechanikai koptató hatása/
- abrázió / áramló folyadékok és az azokban lebegő szilárd részek mechanikai koptató hatása/
- kifáradási korrózió / váltakozó mechanikai, esetleg egyszerre vegyi igénybevétel hatására kialakuló korrózió/
- feszültségi korrózió / fémek hideg átalakítása vagy hegesztése közben kialakult, belső húzófeszültség okán fellépő káros szerkezeti változások (pl. repedések)/
- kapilláris korrózió /üregekben, illesztésekben és hézagokban keletkező károsodási folyamat/
Festékbevonatokkal a korrózió ellen!
Tekintettel arra, hogy összefoglalónk elsődlegesen a korrózióvédelem festékbevonatok kialakításával végzett korrózió elleni védelmet tárgyalja, nézzük meg, milyen fontosabb korróziós tényezők hatásmechanizmusai érhetik a védőbevonatokat. Fontos tényezők ezek, hiszen a korróziós hatás és a védeni kívánt felület között kizárólag a bevonat áll majd, így ezekkel a hatásokkal és tényezőkkel a bevonatnak kell megküzdenie. Lássuk mik ezek és hogyan támadnak!
- Légköri vagy klimatikus tényezők lényegében az időjárásra jellemző levegő állapotát kialakító fizikai sajátosságok. Ilyen lehet a
- Levegő hőmérséklete, amely hazánkban is (amely mérsékelt égövi) igen széles határérték között változik. A hőmérséklet ingadozás a festékbevonatok elöregedését, rugalmasságának csökkenését idézi elő. Jelentős az alap pórusaiban lévő vízgőz és levegő hőingadozás hatására történő kiterjedése és összehúzódása, amely gyakorlatilag lefeszítheti a festékbevonatot. Így a nem kelően telített pórusú felületről a festékbevonat leválhat. Fontos körülmény a festékbevonatok hőelnyelése is, hiszen egy hőelnyelő (mondjuk fekete színű) festékbevonat 30 °C-os hőmérsékleten akár 60-65 °C-ra is felmelegedhet. Ugyancsak fontos tényező a
- Páratartalom is, amely a festékbevonat folytonosságát kezdheti ki. (hólyagosodás, repedezés) Ha a bevonat alá nedvesség férkőzik, akár pára formában vagy fagy hatására, az a bevonat a felületről történő leválását eredményezheti. De ugyanilyen káros lehet a túlzott és erős
- Napsugárzás is, amely az erős UV sugárzás okán a színtelen lakkokat és a sötét bevonatokat erősebben károsíthatják, gyorsítják elöregedésüket. Nem elhanyagolható a
- Légmozgás (szél) károsító hatása sem, különösen, ha magas (szilárd) szemcsetartalommal párosul.
- A Vegyi jellegű korróziós tényezők körébe tartozik az ipari környezet okozta szennyeződések összessége. Ezek eredményeként a felületet érő kén-dioxid, kén-hidrogén végső oxidációs termékként kénsavas anyagként károsítják a festékbevonatokat. De ide sorolhatjuk a savas eső hatását, vagy a sós (pl. útszóró só) közeg okozta korróziós hatásokat.
- A Mechanikai tényezők jelentős hatással vannak a koptató igénybevételnek kitett festékbevonatok tartósságára. Ilyen hatásoknak vannak kitéve a folyadékokat szállító csővezetékek, silók, vegyipari berendezések, de az olyan egyszerűbb felületek is mint a padlólakkal bevont parkett, vagy a zománcolt fémkorlát.
Az eddig bemutatott korróziós jelenségek leggyakoribb megjelenési formái a következők lehetnek:
- Bemaródásos korrózió: tűszúrásszerű támadási forma, pontkorrózió (pitting). Páradús térben, védőbevonatok pontszerű hibáinál a leggyakoribb.
- Szövetszerkezeti korrózió: változatait (kristályhatár menti, szelektív) a fémek inhomogenitása okozza.
- Repedéses korrózió: nagy húzófeszültség is hat a korróziós folyamattal egyidejűleg. Fárasztó igénybevétel esetén fáradási korrózió.
- Réteges korrózió: kis bemaródásból indul, eltérő összetételű vagy szemcsenagyságú részek határán a felülettel párhuzamosan halad. Kavart vasból készült szerkezeteken gyakori.
- Egyenletes korrózió: többé-kevésbé egyenletes anyagveszteség nagy helyi eltérésekkel, általában száraz gázok okozta kémiai korrózió és elektrolitos oldódás esetén.
- Berágódásos korrózió: súrlódó, koptató igénybevétel esetén szennyezett környezetben a mechanikai és vegyi hatás egymást erősíti. Fárasztó igénybevételnek kitett szegecs- vagy csavarkapcsolatoknál, saruknál, csuklóknál gyakori.
Akkor hogyan tovább?
Megismertük a fémek ellenfeleit és innen a feladat „egyszerű”. Meg kell védenünk a felületet a fent részletezett veszélyektől, meg kell akadályozni a korrózió kialakulást. Az első lépés ehhez, hogy pontosan tudjuk, hogy milyen felület az, amit védelmezünk és milyen korróziós hatásokra számíthatunk. Természetesen a szabványkönyvek (most éppen a MSZ EN ISO 12944 sz. szabvány) itt sem hagynak cserben minket és 6 kategóriába sorolják a korróziós környezetet.
C1 – jelentéktelen. Ez nagyjából egy fűtött, állandó hőmérsékletű épületet, szállodát, bevásárló központot, irodaházat illetve ezek belterét jelentik.
C2 – csekély. Ez külső környezetben enyhe légköri szennyezettséget jelent. Belső terekben olyan fűtetlen épületeket, ahol a hőmérsékletváltozás kondenzációt okozhat, pl. raktárak, csarnokok.
C3 – jelentős. Külső környezetben városi és ipari légkört jelent, ahol jelentős mennyiségű kéndioxid fordul elő. Tengerpart közelében enyhe sós pára-terhelést jelent. Belső terekben, mint üzemekben, ahol magas a páratartalom és enyhe levegő-szennyezettség is jelentkezik, pl. sörgyár, tejüzem, húsüzem, ipari mosodák tartoznak ebbe a kategóriába.
C4 – erős. Külső Ipari környezetben, valamint tengerpart mellett, ahol erős sós páraterhelés is fellép. Belső terekben ez vegyi anyagok jelenlétét feltételezi a levegőben, pl. vegyipari üzemekben, uszodákban, stb.
C5-I – nagyon erős ipari igénybevétel. – Külső térben ez olyan Ipari környezetben tapasztalható, ahol magas a páratartalom, vagy a levegő agresszív vegyi anyagokat tartalmaz. Belső területeken pedig olyan épületrészeknél, valamint területeknél, ahol a levegő szennyezett és állandó a páralecsapódás.
C5-M nagyon erős tengeri igénybevétel – Külső térben ez nem mást jelent, mint tengerparti és partközeli területeket, ahol állandó a sósvizes igénybevétel. Belső térben pedig olyan épületrészeknél, valamint területeknél, ahol a levegő szennyezett és állandó a páralecsapódás.
Miután kiismertük a környezeti veszedelmeket, amelyek a korrózió képében csapnak le fémfelületeinkre, a védelmi stratégiát kell kidolgozni. Alapvetően bármilyen védelem is amit választunk, fontos, hogy a védeni kívánt felület legyen tiszta. Ugyanis a szennyezet felületre nem tudjuk a védelmet megfelelően ráépíteni, ezáltal a korrózió a szennyeződések körül, mint sok kis partizáncsapat kezd el tevékenykedni a védelmi vonalaink mögött.
A fémfelület legyen tiszta, szennyeződés és főleg rozsdamentes. Ez elérhető sok módszerrel, illetve néhány kémiai átalakítást is elvégző alapozó nem is igényli annyira a tiszta felületet. Ugyanakkor a legtisztább az, ha tiszta felületre visszük fel a korrózióvédelmet és nem a modern kémia összes csodájára számítunk.
Lássunk néhány felülettisztító illetve előkészítő módszert:
- Mechanikai oxidmentesítés lehet szemcseszórás (kvarchomokkal), drótkefézés (kézi vagy gépi), termikus oxidmentesítés (lánggereblyézés)
- Zsírtalanítás: lúgos oldat, szerves oldószer, vízgőzsugár alkalmazása
- Kémiai oxidmentesítés: savban vagy sóolvadékban áztatás
- Felületi tapadás növelése, például foszfátozás
Az alapozó
A megfelelő felületvédelem alapja az alapozás. A megfelelő alapozó alapozza meg a hosszú védelmet. Az alapozók rendeltetése, hogy megfelelő tapadást és a szívó képességet biztosítson. Tekintve, hogy a fémfelület nem rendelkezik szívó képességgel, ezért a szép és színes festékek, nem tapadnak meg a felületen.
A fémalapozóknak alapvető feladatuk, hogy a felületet szívóképessé tegyék, ezért pigment tartalmúak. A gyártás során nagy szemcséjű, nedvszívó képes pigmenteket alkalmaznak, mint a bauxit vagy az oxidvörös pigmentek. Ezek az anyagok szárazak az olajszámuk csekély.
A könnyű-fémalapozók anyagában a különböző marószerek (mint a foszforsav) megtalálhatók, mint vivőanyagok. Ezek a fémfelültet megmarják, és a marásnyomokba beépítik a pigment anyagot, így egy masszív nedvszívó alapot képeznek a filmrendszernek.
Fémfelület alapozók rendeltetése, hogy a felület és a következő réteg közt megfelelő kapcsolatot, tapadást biztosítson, és felépítése miatt még más egyéb funkciókat is teljesítsen. Ezek lehetnek acél- és vas felületalapozók, illetve könnyűfémfelület alapozók, valamint pigment tartalmuk miatt lehetnek nem passziváló, illetve korrózió gátló alapozók. A nem passzíválló pigment tartalmi fémalapozók kimondott funkciója az alapozás, és nem rendelkeznek korrózió gátló képességgel, általában csak tapadó hídként szolgálnak.
Vannak alapozók, amelyek korróziós inhibítorokat tartalmaznak. Ezek olyan, a korróziót okozó homogén közeghez kis mennyiségben adagolandó kémiai anyagok, amelyek a korróziót gátolják. Ezek reagálva a fémmel képesek visszaállítani a fém felület megsérült oxidrétegét.
A passzívázó alapozók elzárják a fémfelületet, mintegy saját testükkel óvva a fémfelületet a korrózió hatásaitól. Az alapozótól elvárás, hogy mindezt a lehető legvékonyabb rétegben valósítsa meg, hiszen az esztétikai festés és az esetleges további töltőrétegek mind-mind növelik a rétegvastagságot.
A Budaprimer.hu csapatának nem részrehajló véleménye, hogy a BUDAPRIMER alapozó a passzívállók mezőnyében kiemelkedő tehetséggel rendelkező „védőjátékos”. Ugyanis nem csupán ráépül, hanem foszforsav tartalmának köszönhetően be is épül a kezelt fémfelületbe, amely segítségével a korróziógátló anyagát (amely éppolyan titkos mint, mint a boltíves hamburgercég óriásszendvics-szósza) egyesíti a fémfelülettel, amely kötést az epoxi gyanta tartalma pecsételi meg.
A BUDAPRIMER ugyanakkor olyan vékony, akár egy fátyol, így az alapozott fémfelület nem veszíti el megmunkálható képességét, így az hegeszthető és vágható marad.
Legyen alap, hogy az alapozó BUDAPRIMER!
A rozsdamentes fémfelület eléréséhez jó munkát kíván a Budaprimer.hu csapata!